ISO 9001:2015 Audit Checklist
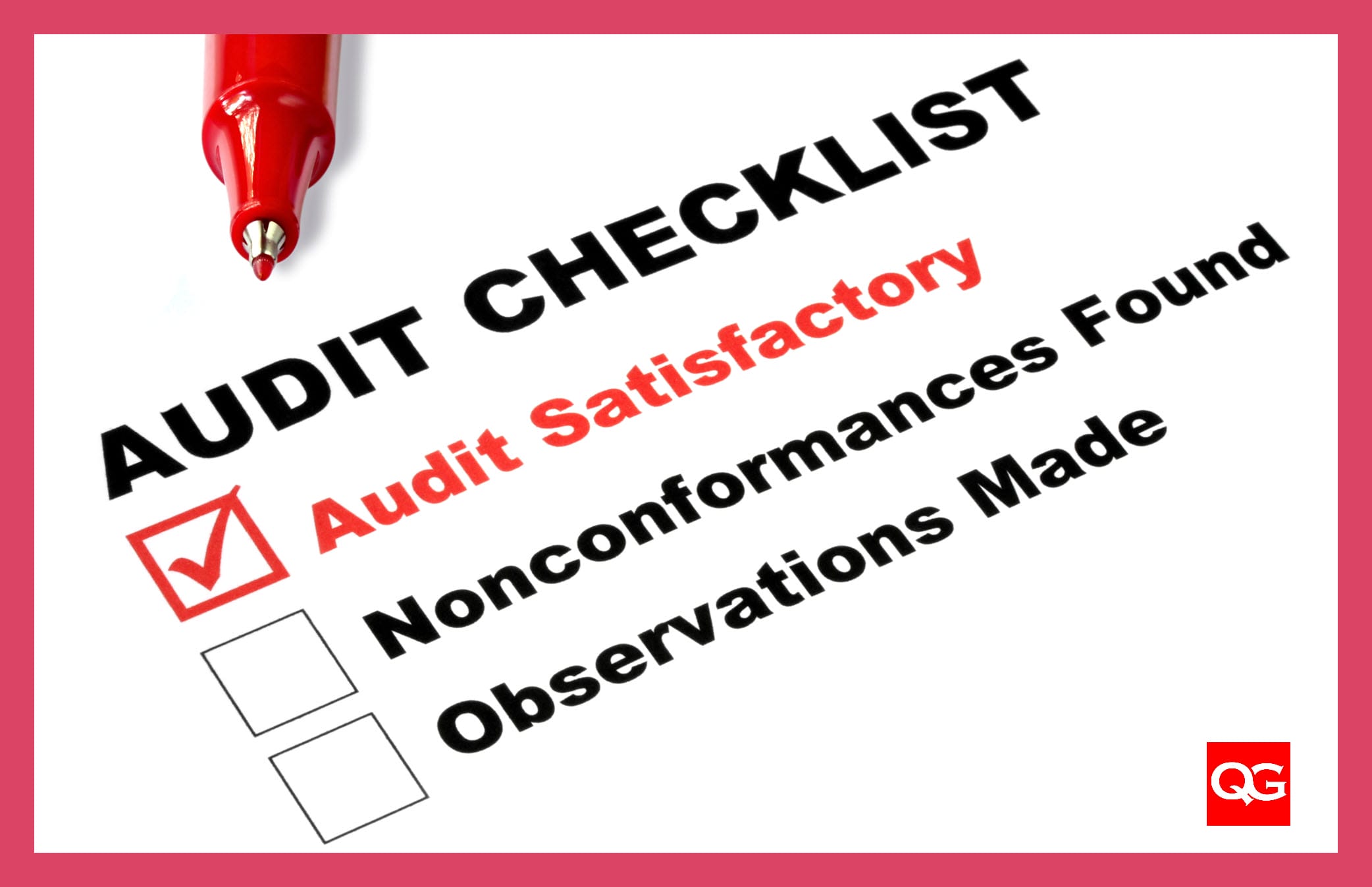
ISO 9001 is a widely recognized standard for quality management systems aimed at helping organizations ensure they consistently meet customer and regulatory requirements. To effectively implement and maintain an ISO 9001:2015 compliant QMS, periodic internal audits are essential for identifying areas of nonconformity and opportunities for improvement. This post will provide a detailed ISO 9001 audit checklist for Clauses 4 to 10. This checklist is designed to be more conversational and systematic, allowing auditors to delve deeper into the implementation level of the QMS. We start from Clause 4 because Clauses 1 to 3 cover general information, normative references, and terms and definitions, which do not require specific audit checks.
4.1 Understanding the Organization and Its Context
- Can you please explain how the organization identifies relevant internal and external issues?
- How often do you review and update these issues? Can you provide examples of recent changes?
4.2 Understanding the Needs and Expectations of Interested Parties
4.3 Determining the Scope of the Quality Management System
- Can you walk me through how the organization defined the scope of its QMS?
- How did you ensure that the scope includes all relevant products, services, and processes covered by the QMS?
- How were the organization's context and the requirements of interested parties considered while determining the scope?
- Is the scope documented and easily accessible to relevant personnel? Can you show me where it is available?
4.4 Quality Management System and Its Processes
- How has the organization established, implemented, maintained, and continually improved its QMS?
- Can you explain how the QMS processes are identified and their interactions determined?
- How do you document process inputs, outputs, sequences, and interactions?
- How were responsibilities and authorities assigned to personnel for QMS processes?
- Can you provide examples of how process performance criteria, resources, and risks are identified and managed?
- How does the organization establish methods for monitoring, measuring, and controlling QMS processes?
- Can you share any recent evaluations of QMS processes and improvements made as a result?